Germany
July 6, 2016
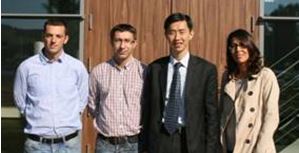
"Our fields of activity in this project were mostly with the design and planning of the system, the acquisition of materials, supervision of assembly, and putting the complete facility into operation“, reports Jean-Renaud Valette (second from right), Office Manager of PETKUS France (Paris). The French team consists of (from left to right), Pierre Lion, Laurent Château and Sana Brirmi.
Ecology promotes technology: in the harvesting of organic produced grains, one encounters a number of weeds and other impurities. This creates many challenges for cleaning machines downstream. In particular, the cleaning of soya beans easily clogs the screens, because the crop has a high percentage of hulls. Efficient and powerful cleaning is thus no longer possible. That’s why farmer Jean Christophe Chassaigne from Moncrabeau, France, has been using the A 09 Agri Cleaner from the German technology manufacturer PETKUS due to its innovative technology. Outfitted with screens connected in parallel, it is able to clean 20 tonnes of impure grains per hour. At the same time, the screens are kept clean with an additional revolving scraper. Together with the ZA61 indented cylinder, the grain cleaner is part of a complete processing plant that meets the needs of organic farming.

Around the five silos, PETKUS also installed a WS1500-8 continuous flow dryer, BE 180 bucket elevators, TKF 200 chain conveyors and an intake pit. The processing line consists of an A 09 cleaner and a ZA61 indented cylinder.
Since 2015, Chassaigne has been working according to the principles of organic farming. The technological needs of this type of production led him to have PETKUS create a customised system for his special requirements. In addition to a silo complex made up of five silos, each with a 160-tonne storage capacity, there is also a sorting line, consisting of an A 09 Agri Cleaner, with parallel connected screens and an additional revolving scraper, as well as a ZA61 indented cylinder. The plant can clean 20 tonnes of extremely impure grain per hour. Thanks to the revolving scraper, inhomogeneous items are spread evenly over the screens in order to guarantee that the entire surface of the screens is used. The farmer thus benefits from a high cleaning capacity and excellent quality.
"In order to efficiently use your screens, the most complete screen cleaning possible is necessary", explains Jean-Renaud Valette, Office Manager of PETKUS France (Paris). Together with Laurent Château, Technical and Engineering Manager (Chalais), he was one of the project managers in Moncrabeau. With an open screen surface of approximately 35 to 45 percent, with perforated screen surfaces, every long-term clog leads to a drastic reduction in separation efficiency. As a result of this, PETKUS outfits its cleaners with a revolving scraper in addition to the ball cleaning method and is the only company in the industry to do so.
In the extensively used ball cleaning method, rubber balls with 20 to 30 mm in diameter are in permanent motion in the trays under the screens due to the vibration of the screen compartment. The impact of the balls causes clogged grain to be released. However, a relatively large screen area near the edges of the ball trays remains uncleaned, because it cannot be reached by the balls. Depending on the size of the ball trays and the diameter of the balls, this area can be up to a quarter of the open screen area. "In the case of soya beans, the impact force of the balls is not strong enough to remove the hulls from the perforations. In addition, the effectiveness of ball cleaning is limited at low screen frequencies and extremely low operating temperatures", explains Valette.

Thanks to the revolving scraper of the A 09 Agri Cleaner, inhomogeneous products are evenly spread over the surface of the screens so that the entire surface of the screen is used.
Better cleaning results for highly impure grains with revolving scrapers
Cleaning with revolving scrapers is a special form of upper screen cleaning in which plastic scrapers that are connected to a rotating link chain efficiently remove long contaminants like stems and pieces of straw from the upper screen. This is extremely important in organic farming, due to the higher degree of debris and foreign materials such as string. In addition to cleaning the screen, the revolving scraper operates as a crop flow regulator that optimally spreads crops that do not flow easily as well as products that do roll easily, across the surface of the screen.
Cleaning the grains is essential for improving the product quality within the processing chain. Large as well as small impurities, foreign materials, shrivelled (grains) and broken grains are carefully and thoroughly removed. The compact and robust medium-output cleaner, which has a capacity of approximately 20 tonnes an hour, can be used for pre- and intensive cleaning as well as seed cleaning. The high quality of cleaning is attained by a combination of linear oscillating screens and an air aspiration system. The screen frames are made of aluminium and the screen compartment is made of three screen layers and a working width of up to 1,200 mm.
The creation of a complete system
Chassaigne originally worked as a logistics manager. He became aware of the PETKUS Group in 2012 when he decided to operate an organic farm 50 km south of Agen with wheat, soya, maize and sunflowers. For his farm, he required a grain cleaning machine with a throughput of one tonne per hour. It quickly became clear that
Chassaigne needed more efficient equipment. Within a year and after multiple meetings, project plans for a complete industrial system were set, with intake, recording, storage and processing that included a cleaner and an indented cylinder. "First, I planned for just a year for this project", reported Chassaigne. "Then I talked to a number of colleagues about organic grains and also what equipment is necessary in order to effectively manage a farm."
In the middle of 2014, there was another meeting between Chassaigne and Valette, because the farmer wanted to add higher storage capacity and a grain dryer. In September 2014, the first machines and devices were transported to France from the PETKUS factory in Wutha-Farnroda, Germany. In addition to the A 09 cleaner and ZA61 indented cylinder, a WS1500-8 continuous flow dryer, TKF 200 chain conveyors and BE 180 bucket elevators were also delivered. An intake pit and a storage facility with five silos, each with a storage capacity of 160 tonnes, completed the facility.
Throughout the entire project, the ecological farmer was intensively accompanied by the technology developer. PETKUS produces its machines exclusively in its own factory in Germany and offers its customers complete solutions. Chassaigne profited from this expertise: "PETKUS supported me not just when getting a construction permit from the responsible authorities which took over a month, but also took over the field inspection, communication with state authorities on the spot, the negotiation with the supplier of the metal construction, as well as planning the assembly with the responsible company and the provision of information for the electricians". The system was designed in close cooperation with and based on the wishes and needs of the farmer. "Our field of activity in this project was the design and planning of the plant and the technology used, the supply of materials,
the supervision of installation and the complete commisioning", adds Valette. In Moncrabeau, since November 2015, organic products have been produced with the highest quality standards and latest technology.
Flexibly planned system allows for additions in the future
The greatest challenge for the PETKUS Group has always been convincing its customers that the entire system is a living process. "We encouraged Mr Chassaigne to already look at the future during the construction of the plant, so that there are possibilities for flexible solutions in changing conditions", reports Valette. "Due to our years of experience, we know what aspects especially need to be taken into consideration in order to operate flexibly." For example, from the beginning, the experts recommended implementing pneumatic rather than manual valves, square silos with profile walls instead of round metal silos, and to use Redler chain conveyors instead of traditional chain conveyors.
Chassaigne is very happy with the implementation of his ideas through PETKUS. "In particular, the cleaner is easy to use and very efficient with regard to the impure organic grain", says the farmer. After he was won over by PETKUS’ comprehensive work, he recently asked about an expansion of his storage capacities and adding a gravity separator to his processing line.
Jean Christophe Chassaigne, who once worked as a logistics manager for various supermarket chains, decided to start producing grain in 2012 as an agricultural beginner. He let PETKUS build a facility in Moncrabeau, 50 km south of Agen. Since then, on 500 hectares, Chassaigne has been producing grains based upon the principles of organic farming. Soya beans, maize, millet and sunflower seeds are also planted, harvested, cleaned and stored.
The PETKUS Group traces its roots back to the farm machine producer Christian Friedrich Röber, who created the first seed treatment machine in 1862, with the goal of minimising post-harvest losses and improving seed quality. Originally on the market as the RÖBER company, the company name PETKUS originated in 1862, when the founder built the first cleaning machine for the rye grower Ferdinand von Lochow III from the manor PETKUS in Brandenburg. In 1883, sons Carl and Rudolf Röber took over the company and increasingly specialised in seed cleaning. During the division of Germany, a spin-off was created from the nationalised organisation, which was united with the original company in 1994. While the company primarily became famous in its early years due to its machines for processing grain and seeds, in recent years, the product portfolio of the PETKUS Group has been moving towards the conception of complete lines for processing and preparation, all the way to the construction of complete plants. Since 2004, the company has listed double-digit rates of growth each year and since 2010, has annually employed 10 to 15 new employees. Currently, there are over 350 employees from over 20 countries employed in 24 offices worldwide.